Особенности вибрации ГА №2 СШГЭС. Дискуссия
© Миша Маклаков
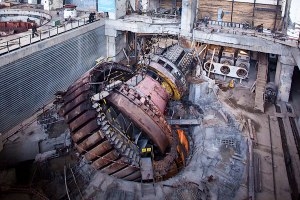
В редакцию Тайги.инфо пришло письмо от сотрудника Саяно-Шушенской ГЭС, ведущего инженера станции Александра Клюкача. В материале он рассказывает об особенностях вибрации гидроагрегата №2, в частности, о том, что на крышке турбины фиксировались высокие частоты, источником которых являются лопатки направляющего аппарата.
В редакцию Тайги.инфо пришло письмо от сотрудника Саяно-Шушенской ГЭС, ведущего инженера станции Александра Клюкача. В материале он рассказывает об особенностях вибрации гидроагрегата №2, в частности, о том, что на крышке турбины фиксировались высокие частоты, источником которых являются лопатки направляющего аппарата.Автор статьи «Клин в мозги?» высказал предположение о том, что причина возникновения трещин в шпильках связана с вибрациями высокой частоты и низкой амплитуды, и назвал при этом источником колебаний вихри Кармана, образующиеся на выходных кромках рабочего колеса. Вероятно, он имеет в виду отчеты Ленинградского металлического завода об исследованиях высокочастотных пульсаций давления воды в области выходных кромок лопастей рабочего колеса СШГЭС. Хотелось бы дать дополнительную информацию: при вибрационных измерениях на крышке турбины, проводимых лабораторией технической диагностики СШГЭС, фиксировались высокие частоты — порядка 200 Гц. Источником высоких частот на крышке турбины являются лопатки направляющего аппарата.
Немного истории
При отыскании наиболее информационных мест для периодических измерений вибрации гидроагрегата передвижным виброкомплексом датчик вибрации установили на верхнюю цапфу лопатки направляющего аппарата (направлением измерения в сторону оси вала агрегата) См. Рис.1:

Амплитудно-частотный спектр вибрации привлек к себе внимание. Это была «лопастная частота» 38 Гц и ее гармоники 76, 152, 190 Гц. См. Рис.2:

Мы обследовали направляющий аппарат всех машин. При измерениях был принят параметр измерения – виброскорость. На амплитудно-частотном спектре виброскорости исследуемая полоса для анализа представлена наиболее удобно.
На большинстве агрегатов лопатки с высокими уровнями вибраций располагались хаотично. Два агрегата – ГА №2 и ГА №6 выделились из общего ряда. ГА №6 не имел в то время лопаток с вибрациями лопастной частоты. На рабочем колесе этого агрегата было выявлено наименьшее число трещин по сравнению с другими.
ГА №2, имея штатное рабочее колесо, отличался тем, что лопатки с высокими уровнями виброскорости лопастной частоты и ее гармоник были по всему периметру. При этом выделялась группа со стороны правого берега – с №7 по №14. На турбинном подшипнике ГА №2 и ГА №6 были высокие уровни «оборотной» (основной) частоты вибрации порядка 100мкм, вызванные гидродинамическим небалансом.
Практическое применение результатов измерений вибрации лопаток направляющего аппарата (38 Гц)
На всех агрегатах ГЭС были выявлены лопатки с высоким уровнем виброскорости «лопастной» частоты. На таких лопатках при разборке верхних подшипников были обнаружены разрушения втулок.
Подшипник – это втулка с антифрикционным стеклоэпоксидным слоем. Понятно, что разрушение втулки — это нарушение а0, расстояния между соседними лопатками, и, как следствие, нарушение равномерного поля скоростей подвода воды к рабочему колесу. Это приводило к увеличению вибраций на гидроагрегатах, увеличению переустановочных усилий в кинематике управления лопатки. Могло привести к заклиниванию лопатки. Мы выявляли до восьми лопаток с разрушенными подшипникам на агрегате. В результате было принято решение о замене подшипников на новый тип из антифрикционного материала Тордон SXL. Это послужило началом капитальных ремонтов с полной разборкой агрегатов. Только так можно было добраться до нижнего подшипника лопатки.
Гидродинамический дисбаланс
Это нарушение симметричного распределения давления на боковой поверхности радиально-осевой турбины, приводящее к появлению переменной возмущающей силы на рабочем колесе.
Проблема гидродинамической неуравновешенности рабочих колес актуальна и сложна. Сложна недостаточностью изученности динамических процессов в гидротурбине. В статье сделана попытка по вибрационным измерениям определить механизм образования и формирования динамических нагрузок на лопастях рабочих колёс, определить причину гидродинамической неуравновешенности на ГА №2.
Причины гидродинамической неуравновешенности:
1. Рабочее колесо.
2. Проточная часть агрегата.
Причина первая. Накопление технологических отклонений в лопастной решетке рабочего колеса. Дефект можно внести при проектировании, изготовлении, эксплуатации. Так, во время эксплуатации рабочего колеса наплавки по устранению кавитации, устранению трещин приводят к изменению геометрии входной и выходной кромок, толщины лопастей, радиусов галтельных переходов. Это не улучшает геометрию лопасти. Хотя при наплавках для контроля применяются шаблоны профиля лопастей турбины, сделанные заводом изготовителем рабочего колеса. Некачественное изготовление вызывает перераспределение статических нагрузок между лопастями. Нагрузки на лопастях, расположенных друг напротив друга, не будут уравновешиваться. И этот небаланс передаётся через воздействие вала на подшипник, т.е. на неподвижные конструкции агрегата [3].
Вторая причина — проточный тракт. Она вызвана динамической нагрузкой, связанной с влиянием ассиметрии подвода воды к рабочему колесу:
- направляющий аппарат (заклиненная лопатка или ее рассогласование);
- спиральная камера не обеспечивает равномерное поле скоростей потока воды на входе в направляющий аппарат и в проточной части турбины;
- лабиринтные уплотнения (при эксцентричной расточке).
Если в зоне идеально сделанного рабочего колеса поток неравномерен, то при вращении рабочего колеса лопасть будет испытывать переменные нагрузки. В результате образуются трещины на лопастях рабочего колеса [2]. Структура и значение динамических нагрузок определяется видом и величиной неравномерности потока.
В случаях 1, 2 мы будем видеть высокий уровень «оборотной» вибрации на турбинном подшипнике.
На сменном рабочем колесе гидроагрегата №2 промышленные исследования [1] выявили высокий уровень вибрации турбинного подшипника с «оборотной» частотой (2,38 Гц). Результаты выполненных исследований указывали на наличие гидродинамической неуравновешенности на рабочем колесе, которая возрастала с увеличением открытия направляющего аппарата и достигала наибольшего значения при полном открытии. Сила гидродинамической неуравновешенности воздействовала с «оборотной» частотой и увеличивалась с повышением напора. Был сделан вывод, что это небаланс рабочего колеса, и он связан с односторонним накоплением технологических отклонений в лопастной решетке, хотя сами отклонения находились в допустимых пределах.
Для снижения уровня небаланса и, соответственно, нагрузок на турбинный подшипник использовались различные способы:
- установка дополнительной массы, действующей в противофазе с силой гидродинамического дисбаланса на спицу ротора генератора (положительного результата не добились);
- установка груза (пластины) на нижнем ободе рабочего колеса. При высоких напорах, в данном эксперименте произошло увеличение усилий на турбинный подшипник более чем в два раза;
- установка пластин в межлопастное пространство привела к возникновению дополнительной гидродинамической силы, которая значительно превышала компенсирующую силу от установленного груза. Соответствующим подбором местоположения и величины груза удалось снизить действующее на турбинный подшипник усилие при определенном напоре. Но при низких напорах гидродинамическая сила изменяла свое направление (на 67 градусов против направления вращения агрегата) при неизменном открытии направляющего аппарата.
Установка штатного рабочего колеса в 1986 году не избавила гидроагрегат от дисбаланса на рабочем колесе. Динамика повышения вибрации на турбинном подшипнике приведена на Рис3. Рабочее колесо ГА №2 выделилось относительно других повышенным трещинообразованием, высоким уровнем «оборотной» (основной) составляющей вибрации на турбинном подшипнике. Так, с 2004-го по 2009 год величина «оборотной» составляющей вибрации стабильно держалась 100-120 мкм, что по «Приложению И» к СТО 1730028227140001-2006 оценивается как «удовлетворительно». Рис. 3:

Совпадение, что на один и тот же агрегат установили подряд рабочие колеса с накоплением технологических отклонений в лопастной решетке, маловероятно.
Выполнив анализ полученной картины распределения высокочастотных вибраций на всех лопатках направляющего аппарата ГА №2 напрашивается вывод, что источником гидравлической неуравновешенности является не рабочее колесо, а спиральная камера, не обеспечивающая равномерное поле скоростей потока воды на входе в направляющий аппарат. На агрегате №2 мы имели группу лопаток со стороны правого берега с высоким по отношению к другим лопаткам уровнем «лопастной» частоты вибрации. Предположив, что поток воды, походя мимо лопатки направляющего аппарата, встретив на своем пути лопасть рабочего колеса, получает импульс и этот импульс отражается на лопатке направляющего аппарата. Чем больше скорость воды данного потока, тем больше воздействие на лопатку, и на ней выше уровень амплитуды вибрации лопастной частоты по отношению к другим лопаткам, где скорость воды ниже (в работах [2,3] доктора технических наук Виктора Ивановича Григорьева показаны исследования более сложных формы влияния неравномерности «кромочного следа» лопатки).
Был произведен эксперимент по выравниванию поля скоростей потока воды. На шести лопатках, у которых наблюдались повышенные вибрации, уменьшали открытие до такого до положения, когда вибрации лопастной частоты уменьшились до уровня среднего значения (по лопаткам данного агрегата), не меняя открытия направляющего аппарата остальных лопаток. В результате на турбинном подшипнике «оборотная» вибрация уменьшилась со 170 мкм до 90 мкм. Биение вала — с 250 мкм до 80мкм при нагрузке Р = 580МВт. При этом следует подчеркнуть, что на данном агрегате турбинный подшипник имел большие зазоры, так как эксперимент проводился перед капитальным ремонтом.
К сожалению, формуляр измерений открытий в выставленном положении лопаток направляющего аппарата во время эксперимента показал, что разброс а0 выше допустимого. Не просматривалась возможность при данной конструкции направляющего аппарата обеспечить заданное рассогласование лопаток и их синхронное закрытие. Применить в эксплуатации результаты этого эксперимента не получилось.
Анализ амплитудно-временной характеристики выбега агрегата (сброса нагрузки), позволяющий выявить критические условия работы на переменных оборотах — резонансные и критические частоты вращения и дает дополнительную информацию при диагностировании таких дефектов как ослабление крепления конструкции, дисбаланс. Осциллограмма сброса нагрузки для данного вида неуравновешенности агрегата №2 имеет характерный вид и приведена на Рис 4:

Другой пример — гидроагрегат №6. Картина распределения амплитуд вибраций лопастной частоты здесь другая. Лопастной составляющей спектра практически нет. Трещин на лопастях рабочего колеса по сравнению с агрегатом №2 раза в три меньше. Но также имеется высокий уровень «оборотной» вибрации, сопоставимый с уровнем вибрации агрегата №2 - 90мкм в радиальном направлении на турбинном подшипнике. Осциллограмма сброса нагрузки гидроагрегата представлена на Рис.5:

Скорость нарастания амплитуды вибрации значительно выше. Гидравлическая неуравновешенность в данном случае на рабочем колесе вызвана накоплением технологической ошибки наплавки лопастей. На рабочем колесе необходима компенсация небаланса.
Разрушающее действие колебаний высоких частот (190 Гц)
Исторически сложилось так, что вибрации гидроагрегатов оценивались по уровню виброперемещений опорных узлов. Это, в первую очередь, связано с необходимостью выявления составляющих спектра и субгармоник, которые у гидроагрегатов обычно находятся в диапазоне частот 0.3-5 Гц. Есть нормы, определяющие допустимую вибрацию в диапазоне частот 1 до 30 Гц. Однако на практике часто имеют место случаи, когда необходимо оценить степень опасности вибрации с более высокими частотами, например, связанными с появлением вибраций лопастной частоты турбины при сходе вихрей. Эти вибрации появляются на частотах свыше 30 Гц и могут достигать по частоте 200-300 и более Гц.
Причем амплитуды этих составляющих вибраций очень малы и на них не всегда обращают внимание. Как показывает анализ литературы [4], напряжение, возникающее в деталях машин под действием вибрации, прямо пропорционально виброскорости:

Иными словами, предел усталостной прочности материала в случае воздействия вибрации более высокой частоты снижается.
Исходя из вышесказанного, возможно, колебания на этих частотах лопаток направляющего аппарата разрушали не только подшипники лопаток направляющего аппарата. Эти двадцать молоточков весом по четыре тонны каждый достучались до шпилек крепления крышки турбины и являются авторами трещин на шпильках.
Лопатка направляющего аппарата (190 Гц)
Необходимо проверить, не возникла ли трещина на одной из цапф лопаток направляющего аппарата и спусковым крючком «триггером» аварии стали её обломки.
Вывод — гидродинамическая неуравновешенность на гидроагрегате №2 вызвана неравномерностью поля скоростей, создаваемого спиральной камерой. Это можно устранить. Необходимо найти отличия в форме спиральной камеры, колоннах статора турбины ГА №2 относительно элементов проточных частей агрегатов, не имеющих небаланс на рабочем колесе. Инструмент в настоящее время есть - высокоточное лазерное 3D сканирование.
Литература.
1.Решение проблем Саяно-Шушенского гидроэнерго комплекса.
Статья «Натурные исследования гидроагрегатного блока и сопоставление их результатов с данными лабораторных исследований» Ю.С. Васильев, И.С. Саморуков, И.П. Лисовин, В.И. Григорьев, И.П. Иванченко. Ленинград, 1987г.
2.Григорьев В.И. Исследование неравномерности потока, создаваемой лопатками направляющего аппарата гидротурбины. «Гидротехническое строительство»
3. Григорьев В.И.Механизм образования динамических нагрузок, действующих на основные элементы гидроагрегатов. «Гидротехническое строительство»
4.Исследование и устранение вибрации паровых турбогенераторов. М. Энергоиздат 1982г.
5.Брызгалов В.И., Клюкач А.А. Опыт работы лаборатории технической диагностики Саяно-Шушенской ГЭС. «Гидротехническое строительство» №9, 1998 г.
Клюкач Александр Александрович, инженер.
Ведущий инженер Филиала РусГидро «СШГЭС имени П.С. Непорожнего»
655619. Республика Хакасия, г. Саяногорск., пос. Черёмушки, ул. Саянская, д.1. Домашний телефон - (39042) 33305, 89617400196. Рабочий телефон - (39042) 71674.
Новости из рубрики:
Последние материалы
26 Сен 2023, 13:29
Хроника текущих событий. Экономика, общество, политика. Выпуск 526
25 Сен 2023, 12:23
Хроника текущих событий. Экономика, общество, политика. Выпуск 525
22 Сен 2023, 11:20
Хроника текущих событий. Экономика, общество, политика. Выпуск 524
21 Сен 2023, 13:19
Хроника текущих событий. Экономика, общество, политика. Выпуск 523
20 Сен 2023, 12:18
Хроника текущих событий. Экономика, общество, политика. Выпуск 522