Особенности производства искусственного графита
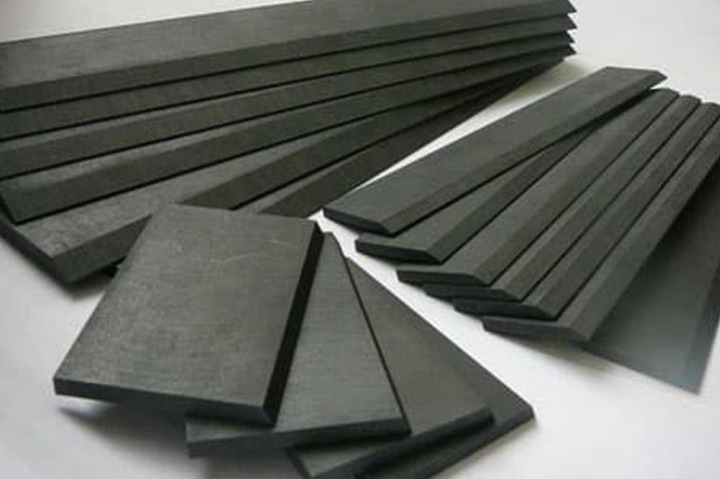
Графит является аллотропной модификацией углерода наряду с алмазом, карбином и аморфным углеродом. Аморфный углерод имеет турбостратную разупорядоченную структуру мелкокриталлического графита. Подобную структуру можно встретить в саже или активированном угле.
Графит – единственная термодинамически устойчивая в обычных условиях аллотропная модификация углерода. Он представляет собой жирное на ощупь вещество от черного до темно-серого цвета с металлическим блеском (в зависимости от дисперсности и происхождения).
Основные морфологические виды графита: чешуйчатый, плотнокристаллический (комовый) и аморфизированный. Чешуйчатые графиты делят на крупно-, средне- и мелкочешуйчатые. Различают их и по толщине чешуйки.
Кристаллы графита имеют слоистую структуру. Атомы углерода в кристаллической решетке графита расположены в углах шестиугольников бесконечных базисных плоскостей, атомы кристаллической решетки расположены слоями, что определяет относительно невысокую механическую прочность. Хорошая электро и теплопроводность связана с высокой плотностью атомов в слоях. При нагревании вещество не плавится, горит только в струе кислорода, а испаряется в вольтовой дуге.
Природный минерал (естественный графит) добывают из вулканических и магматических пород и каменноугольных отложений. Он содержит различные химические примеси: SiO2, Аl2O3, Р2О5, MgO, CuO, FeO, СаО. Но добытого из карьеров запаса не хватает для удовлетворения всех запросов промышленности.
Из минерала делают:
- огнеупорные материалы;
- смазку;
- контакты электрических машин;
- краски;
- карандаши;
- аккумуляторы и батарейки.
Широко используют естественный графит в ядерной энергетике, химической промышленности, при производстве токопроводящей резины, в металлургии (как литьевой материал и источник углерода для сталей и чугуна разных марок). Всю продукцию можно посмотреть в нашем каталоге https://doncarb.com/catalog/
Значительная часть промышленного графита — это искусственный графит.
Искусственные графиты обычно получают из нефтяного кокса (наполнителя) и каменноугольного пека (связующего). Вместо каменноугольного пека в качестве связующего могут быть использованы синтетические смолы, например, фурановые или фенольные. В качестве наполнителей также применяется пековый кокс и антрацит. Все наполнители предварительно подвергаются прокалке при температуре до 1300℃, а затем дроблению, размолу и классификации по гранулометрическому составу.
Грансостав задается в зависимости от назначения графита, затем производится рецептурная дозировка компонентов наполнителя и связующего, при необходимости вводят добавки. Сдозированные компоненты смешивают в смесителях при заданных температурных режимах, подготовленную массу подвергают охлаждению и направляют на формование. Формование заготовок осуществляют методом экструзии или прессования. Полученные заготовки подвергают ступенчатой термообработке без доступа воздуха для карбонизации (до 1300 – 1500℃) и, затем, графитации (до 2400 – 2800℃).
Разновидностью искусственного графита является пирографит, получаемый медленным осаждением на нагретой до 2500℃ поверхности углерода при термическом разложении углеводородов. Пирографит практически не обладает пористостью, ему присуща анизотропия свойств.
Возможно получение искусственного графита методом нагревания антрацита до высоких температур ( 2200℃) без доступа воздуха и некоторыми другими методами.
Для получения искусственного графита с заданными свойствами, графитовый полуфабрикат пропитывают пеком, фенолоформальдегидными смолами и другими веществами. Часто для достижения требуемых характеристик графит подвергают термообработке и пропитке неоднократно.
Полученный разными способами графит отличается по многим параметрам, но обладает и рядом сходных качества. Это повышенная прочность, стойкость к окислению, кислотоупорность, отличная электропроводность. Искусственный графит высокой химической чистоты производится в виде порошка разных фракций. Для получения формовых деталей, порошок прессуют и спекают по специальной технологии.
Самые чистые из искусственных графитов – спектральный и ядерный графиты. Для последних из упомянутых в зависимости от марки содержание основных примесей лимитируется в следующих пределах: зольность – 0,035 –0,170 %; Са – 0,01–0,05 %; Fe 0,01 %; Ti 0,01 %.
Такие высокие требования к чистоте материала обусловлены областью применения.
Использование графита в ядерной технике объясняется следующими его качествами: распространенностью, удовлетворительными замедляющими свойствами и малым сечением захвата нейтронов. Наличие сопутствующих примесей, как правило обладающих высоким сечением захвата нейтронов, значительно ухудшают ядерно-технические свойства графита. Для эмиссионного спектрального анализа используют графит с еще меньшим содержанием примесей (требования к аналитической чистоте материала). Учитывая объем потребности в графите, разработаны разные технологии получения материала, отличающегося химической чистотой, применением, видом кристаллической структуры.
Самые распространенные виды:
- Ачесоновский — получают путем нагревания заготовок, изготовленных на смеси пека и кокса, прошедших карбонизацию в электрических печах Ачесона до температуры 2800 оС;
- Пиролитический — синтезируют из природного газа;
- Доменный — образуется как попутный продукт при охлаждении чугуна;
- Карбидный — получают путем термического разложения карбидов.
ОБЛАСТИ ПРИМЕНЕНИЯ УГЛЕРОДНЫХ МАТЕРИАЛОВ
Объем производства углеродных материалов в стране позволяет судить об уровне ее технического развития. Ракетная техника, космонавтика, авиастроение, металлургия черных и цветных металлов, ядерная энергетика, химическое машиностроение, автотранспорт, судостроение, электроника и медицинская промышленность, производство спортивного инвентаря и многие другие отрасли промышленности получили свое развитие в основном благодаря использованию разнообразных углеродных материалов.
Отличительной особенностью антифрикционных углеродных материалов, к которым относятся изделия из природного и искусственного графита, углерод-углеродные композиционные материалы, является то, что, благодаря слоистой структуре, высокой теплопроводности и удовлетворительным механическим свойствам, они работоспособны в условиях трения без смазки.
Химическая стойкость антифрикционных углеродных материалов зависит как от стойкости самих углеродных материалов, так и от стойкости материала пропитки.
По сравнению с графитом углеродное волокно обладает меньшей теплопроводностью, масса детали из него меньше, и волокно не такое хрупкое. Высокие цены на углеродное волокно российского производства сильно затрудняют их применение во многих отраслях промышленности (строительство, медицина, автомобильная промышленность, спортиндустрия и т.д.).
На данный момент основные потребители углеродных волокон в России – авиакосмическая отрасль и атомная энергетика. Однако уже в ближайшем будущем российские производители планируют значительно увеличить мощности производства, за счет внедрения более совершенных технологий и оборудования, что должно привести к удешевлению продукта и, в конечном итоге, увеличению областей применения.
Где производят графит
Компания ООО «Донкарб Графит» производит изделия из графита для промышленности. В том числе и коллоидный порошок всех возможных фракций (мелкий, средний, крупнозернистый), получаемый методом прошивного прессования, прошедшего первичный и повторный обжиги пропитку и графитацию с особыми свойствами (марка АТМ, ОСЧ МГ, ГМЗ, ППГ и другие. Каталог продукции включает также несколько десятков видов готовых фасонных изделий.