Нефть превращается: путь от НПЗ до бензобака новосибирского таксиста
© Наталья Гредина
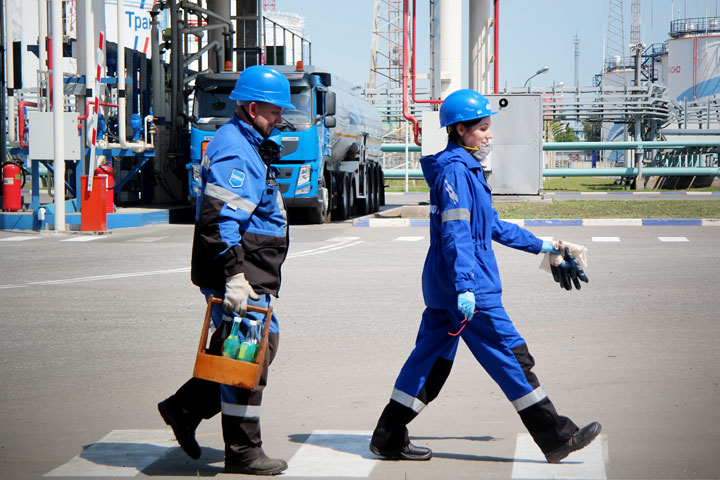
Прежде чем стать бензином и попасть в топливный бак, нефть проходит через сотни операций. Чтобы понаблюдать за полным циклом производства нефтепродуктов, корреспондент Тайги.инфо поехал в Омск — один из самых мощных центров топливной промышленности страны.
Западно-сибирская нефть считается легкой. Содержание серы, от которой вся промышленность ищет пути избавления, в сибирских нефтяных месторождениях составляет всего полпроцента. С этой точки зрения, сибирским нефтяникам сказочно повезло — процесс переработки значительно облегчается. Все этапы сопровождаются контролем качества топлива — это сложный технологический процесс, к которому каждый, через чьи руки проходит нефтепродукт, старается подойти с высокой степенью ответственности.ОНПЗ. Серебряный город
5 сентября Омский нефтеперерабатывающий завод отметит свое 60-летие. Его строительство было задумано в послевоенный период, когда страна искала новые технологические решения для развития промышленности Сибири, Казахстана и Дальнего Востока. В 1949 году было принято решение о создании крупного нефтезавода. С момента запуска первой установки ОНПЗ в 1955 году, в Омск начали перебираться лучшие специалисты cтраны, а заводу предрекали роль флагмана нефтяной промышленности. Так Омск стал городом нефтяников.
Идейный вдохновитель и первый директор ОНПЗ Александр Малунцев приехал сюда из Азербайджана. Согласно свидетельствам современников, на родине ему прочили большое будущее, призывали остаться. Однако он выбрал новое направление и в 1953 году поселился в Омске. Нефтяники и теперь вспоминают его добрым словом — называют «наш первый, харизматичный директор», в музее ОНПЗ благодарные потомки воссоздали кабинет с рабочим столом, чертежами и книгами, когда-то принадлежавшими Малунцеву.


.jpg)

.jpg)
В 2006 году завод вошел в структуру компании «Газпромнефть». Сегодня ОНПЗ перерабатывает 7,4% всей российской нефти, в 2013 году оборот продукта составил 21,3 млн тонн. В 2012 году здесь началась масштабная реконструкция и замена оборудования. Сегодня территория завода занимает 13 квадратных километров, на которых установлены 50 установок разной сложности и площади. Протяженность дорог, соединяющих установки и другие объекты, равна расстоянию от Омска до Большеречья или от Москвы до Твери. Сейчас здесь трудится примерно 2800 сотрудников, по территории завода их ежедневно развозит маршрутный транспорт. Следующая комната музея — ОНПЗ в миниатюре. На территории пока есть пустые места, но, согласно программе модернизации предприятия, к 2020 году они будут заполнены новыми установками.
Мы едем по территории завода на автобусе, слева и справа в окнах мелькают трубопроводы и трубы серебряного цвета. Сверкающий город — установки размером с пятиэтажный дом переливаются на солнце, а над ними возвышаются факелы. Пламя на конце футуристических построек кажется миражом. Без сопровождающих заблудиться в этом лабиринте проще простого. Шарообразные цистерны — сырьевые резервуары, громадные ослепительно-белые цилиндры с надписью «ОГНЕОПАСНО» — хранилища для готового топлива. Мы останавливаемся и выходим около необъятной установки изомеризации легких бензиновых фракций.




Прежде чем стать топливом, нефть проходит череду испытаний. Поступив на завод, сырье отправляется на установки первичной обработки. Там нефть делится на фракции: газ, рефлюкс, бензин, авиационный керосин, дизельное топливо и мазут. Затем каждый из этих «полуфабрикатов» отправляется на свою, индивидуальную переработку. Нестабильная бензиновая фракция отправляется на стабилизацию, где от нее «отгоняют» легкие углеводороды. Затем результат отправляется на вторичную переработку, после которой и получается знакомый нам бензин. Дизельное топливо проходит процедуру «облагораживания» на установках гидроочистки, там его избавляют от серы. В результате получается дизель нового экологического класса стандартов Евро-4 и Евро-5. Мазут и авиационный керосин также проходят этапы очистки. В итоге мазут уходит на приготовление товарных топлив, а авиационный керосин сразу отправляется потребителям, им, например, заправляют пассажирские самолеты.




Глубина переработки характеризует эффективность всего производства. Отношение переработанного сырья к количеству полученного продукта, а проще говоря — уровень безотходного производства, по данным представителей завода в 2014 году составил 93%. Сегодня это также самый высокий показатель по России. Оставшиеся 7% идут на мазуты, которые используются на производстве, поэтому в глубине переработки не учитываются. Уровень чистых отходов, по словам Есикова, составляет 0,5%.
За качеством топлива следит лаборатория технического контроля, которой управляет Юрий Голованов. Все сырье и полученные на заводе продукты проверяется здесь. По словам Голованова, сегодня лаборатория также идет по пути сокращения ручного труда. К 2020 году, когда весь завод планирует выйти на новый технологический уровень, лаборатории надеются почти полностью автоматизировать процесс анализа проб.

.jpg)


Нефтебаза. Хранилище горючего
Рядом с заводом располагается Омская нефтебаза, на которой хранится и отгружается клиентам полученное на ОНПЗ топливо. Объект входит в структуру «Газпромнефть-Терминала». В 2014 году на нефтебазе завершилась масштабная реконструкция, весь процесс отпуска нефтепродукта автоматизирован. Объем перевалки здесь составляет 800 тысяч тонн в год, в день на нефтебазе заливают до 250 бензовозов.
«Мы автоматизировали абсолютно весь процесс — от авторизации водителя бензовоза путем бесконтактной карты до выдачи документов при выезде. В плане комплексной автоматизации мы абсолютно первые и сейчас будем применять этот опыт на остальных нефтебазах. Я думаю, он станет стандартом деятельности в этой области», — рассказывает генеральный директор «Газпромнефть-Терминала» Павел Полищук.
Мы переодеваемся в униформу — все работники и гости предприятия обязаны соблюдать технику безопасности. Территория предприятия включает резервуарный парк, автоматическую станцию налива топлива и операторную. C Омской нефтебазы топливо отгружается клиентам «Газпромнефть-Региональных продаж» и на АЗС «Газпромнефти» по Сибири. Ключевая задача нефтебазы — сохранить количество и заводское качество нефтепродукта. Внедренная после реконструкции автоматизированная система самообслуживания водителей бензовозов значительно оптимизировала процесс перевалки топлива.



.jpg)
Качество нефтепродукта контролирует аккредитованная испытательная лаборатория. Пробы отбираются с каждой партии топлива, поступающей на нефтебазу. Лаборатория анализирует их на 15 показателей — от содержания воды и серы до определения октанового числа. Все результаты отражаются в паспорте качества. Он вывешивается в «уголке покупателя» и на каждой автозаправке «Газпром нефти». При этом образцы проб сохраняют в качестве арбитражных— они необходимы на случай претензий клиентов к качеству топлива.
Перед тем, как покинуть нефтебазу, все отсеки бензовозов снабжаются пломбами, которые могут быть сняты только на АЗС.
Заправка. Как попасть в бензобак
Бензовоз, заполненный на нефтебазе, вместе с необходимыми документами отправляется на одну из городских АЗС «Газпромнефть». Прежде чем приступить к приему топлива, сотрудник станции осуществляет целый перечень строго регламентированных процедур. Сначала — обеспечение пожарной и промышленной безопасности. Бензовоз заземляется — водитель уже подключил его к специальному устройству, которое ликвидирует накопившийся на топливе во время перевозки статический заряд.





Мы тестируем 92 бензин — работник АЗС вставляет раздаточный пистолет в устройство, напоминающее увесистые песочные часы. Оператор задал дозу в 10 литров. Пока они наливались, пистолет, оснащенный системой рекуперации, откачивал испарения — запаха мы не почувствовали. Допустимая государственным регламентом погрешность — не более 50 мл на 10 литров топлива. Здесь мы увидели отклонение лишь на одно деление (около 10 мл). Топливо из уровнемера сливается обратно в резервуар, чтобы, в конечном счете, попасть в бак автовладельцу.




Уже в Новосибирске интересуюсь у таксиста, знает ли он, как и где делают бензин, за которым мы только что заехали на все ту же «газпромовскую» заправку. Просит рассказать про завод, а потом, подумав, подытоживает: «Это хорошо. Еще бы придумали такие дороги, на которых шины не лопаются. Я как раз только из Омска вернулся, в середине пути чуть в кювет не улетел».
Текст и фото Натальи Грединой
Новости из рубрики:
Последние материалы
26 Сен 2023, 13:29
Хроника текущих событий. Экономика, общество, политика. Выпуск 526
25 Сен 2023, 12:23
Хроника текущих событий. Экономика, общество, политика. Выпуск 525
22 Сен 2023, 11:20
Хроника текущих событий. Экономика, общество, политика. Выпуск 524
21 Сен 2023, 13:19
Хроника текущих событий. Экономика, общество, политика. Выпуск 523
20 Сен 2023, 12:18
Хроника текущих событий. Экономика, общество, политика. Выпуск 522